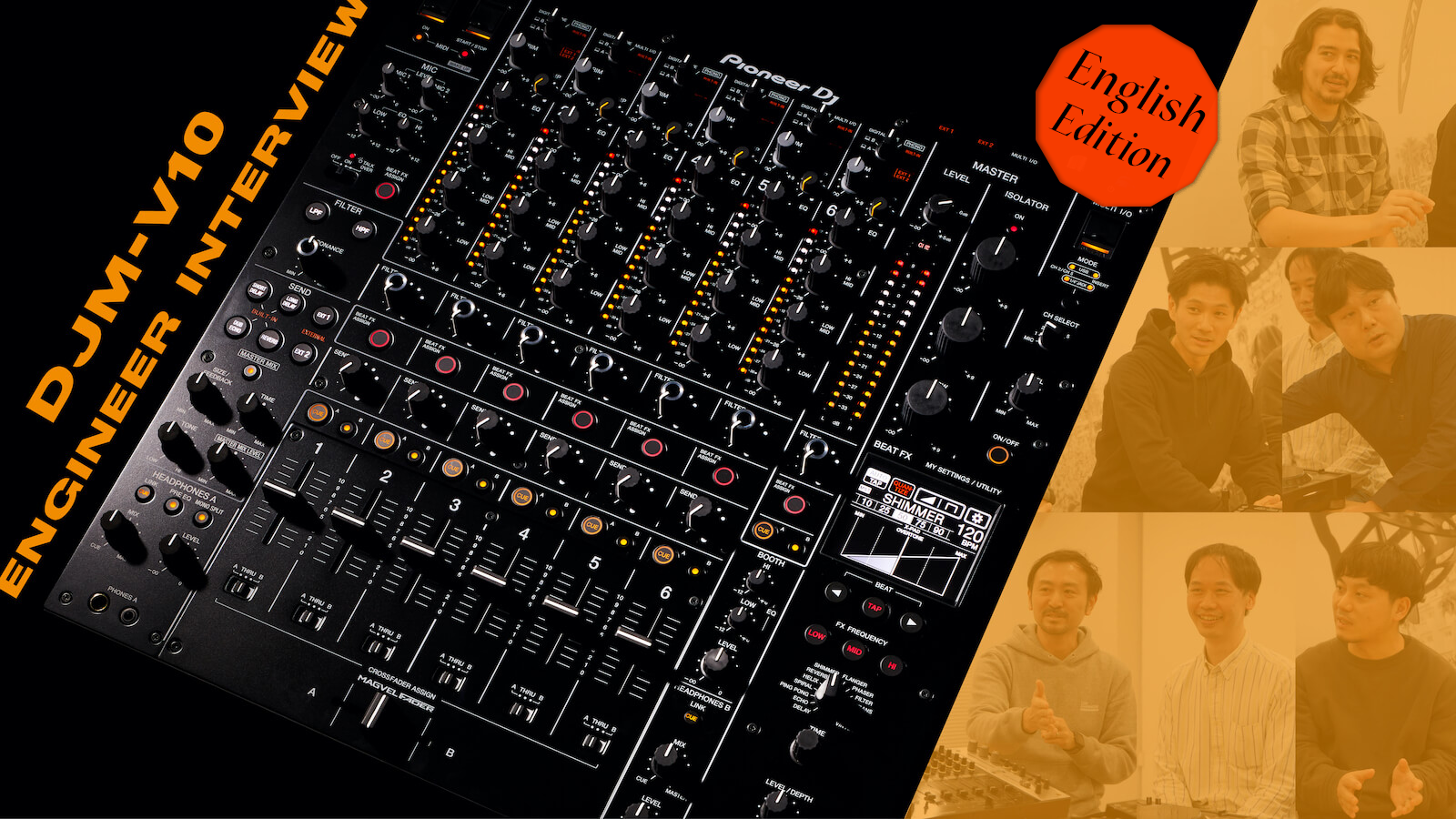
Highlight
Pioneer DJ “DJM-V10” Engineer Interview
Text & Interview : Hiromi MatsubaraPhoto : Shotaro Miyajima
2021.6.16
4-band EQ to layer sounds with multiple channels, Master Isolator to satisfy you with natural mixing
DJM-V10 is equipped with 4-band EQ for the first time on Pioneer DJ mixer, and the first Master Isolator since DJM-1000 released in 2005. We had a switch for EQ and Isolator on recent models like DJM-900NXS2, but what made you separate the two this time?
Montpetit: First, we started hearing opinions that 3-band EQ can’t sufficiently serve for detailed adjustments, as DJ styles diversify and people use more and more sound sources. For example, conventional 3-band EQ can’t perform “killing heavy kicks while emphasizing attacks”. So, we broke it down into 4-band EQ, enabling more detailed adjustments. Another point here is that you can layer your sounds not only with two tracks, but with 3 or 4-channel as you wish.
And now that we considered what you’ll need when you want to sculpt your entire sound, for instance “to kill the LOW quickly after layered everything in a good balance” or “to bring up only the HI”, we decided to introduce Isolator on the Master channel. Then we hammered out the details like how to separate frequency bands, or how to set a degree for each band. So, the background [for these new functions] is that we changed the parts necessary to adapt to diversified DJ styles.
How did you change frequency bands, as 3-band EQ evolved into 4-band EQ?
Koizumi: Until now with 3-band EQ, when you kill the LOW, you lost both kick and base. In contrast, we set frequency bands on 4-band EQ as “LOW for kick”, “LOW MID for base and synthesizer”, “HI MID for clap” and then “HI for high hat”.
And how did you carry on research and development on Master Isolator?
Koizumi: We started by listening to various DJ performances. Then, we compared all the data we had from auditioning isolators; DJ mixers with a Master Isolator have been increasing gradually in the recent years.
Besides our team members, we asked in-house experts and DJs who use isolators in their performances, to touch and listen to different isolators, then let them choose their favorite; based on which, we created a prototype. That prototype being our starting point, we made detailed adjustments, then asked our colleagues to touch and listen to it: a degree of frequencies and Filter curves, how much you can turn on + side… etc. We repeated this process again and again until we finally arrived on the final product. Upon deciding, we particularly focused on making parameters, where isolator helps to create satisfying performances, and that DJs themselves can also enjoy using it.
Shinya Koizumi – Engineering Management Department, Firmware Design Department, Mixer Section
Montpetit: As Koizumi just mentioned, we brought various mixers to our studio once and tried them out. We touched each in a neutral way and bounced off unbiased opinions each other, like “this one feels good”, then we measured “why it felt good” once we brought them back [to the office], after we gathered once again and listen [to mixers] based on the data… it went like that. Fortunately, we have several in-house DJs who use isolators in their performances, so we could get valid opinions by asking them to come and try them out. Since Isolator on DJM-1000 was up to +6, we were also going for +6 while making our prototype. But then, we heard that +6 sometimes can’t give a final touch, especially when house DJs want to emphasize vocals by rhythmically move a MID-Isolator for tremolo effect. Then we tried +9 to meet this type of demand, got very positive reactions like: “yes, this’s it!”, and finally decided to adopt +9 on DJM-V10. But there were some mixers from other brands with even +18. [laugh]
Koizumi: Right, there were some. [laugh] We were like: “wow this’ll be something” and tried them out just in case, but it was too loud to handle.
Sugai: People good at operating isolator can handle +18, but it’s definitely not easy to do the same in DJM-V10’s interface. Taking that into consideration too, we agreed on +9.
Koizumi: We researched [on isolators] quite intensely. Researching for DJM-1000 development was around 2004, and compared to then, usages of isolators are not the same anymore. With numbers of test auditions, it became crystal clear to us that DJM-1000’s style is not sufficient for today’s needs, and we should completely refine it.
Montpetit: Regarding its degrees, when you use EQ Curve switched onto Isolator on DJM-900NXS2, it kills very sharp and crisp. We have feedbacks that this helps a lot when mixing tracks, so we kept it in this way [for DJM-V10], which you can completely kill both LOW and HI until -∞. But while studying other mixers, we realized that things might be different when it comes to an isolator. Then, as we researched thoroughly what kind of isolators can “make you feel good”, it became clear that degrees are more mild [for those isolators]. We exclusively custom-designed degrees in the Master Isolator [in DJM-V10] considering this, enabling natural mixing and comfortable listening experience when used in combination with 4-band EQ. At the end, we redesigned how to divide frequencies, the amount of boost (maximum volume), the curve (change curve of volume), the degree (sharpness), and all that. We are very satisfied for having done everything we could do.
Whether you feel good or not when using an Isolator, do weights of knobs also play a role here?
Nagata: I was in charge of this part. For example, while a channel volume [knob] in a rotary mixer tends to be heavy for mixing sturdily, isolators tend to be lighter in general so that users can move them rapidly. At the same time, some people use them for fine adjustments just like with EQs. To realize high usability for the both ways of using [an isolator] was one of our goals. For that, we discussed whether to incorporate a center-click or not. At first we were going for without a center-click, but considering DJM-V10 can be a club standard model, it would be necessary to clearly know the home position, so finally we decided to adopt [a center-click], followed by another discussion on the strength of the click.
Yuu Nagata – Engineering Management Department, Firmware Design Department, Advanced Product Design Section
Nagata: Isolator on DJM-1000 has a weak center-click and you couldn’t really feel the home position, which we have worked on this time. If a click is too strong on the other hand, it can be distracting. We carefully managed those weight settings. Also, unlike Trim or EQ knobs, this Isolator has mechanical parts on top of normal electric parts in it. It’s not unique to DJM-V10 but when we can’t find the ideal electric parts that meet our aimed usability criteria, we add original mechanical parts to electric parts to adjust a touch feeling. This center-click’s feel was finally decided after comparing to other brands’ products, producing one in various strengths for tests, and hearing opinions in the company.
By the way, is it a design team who suggests the size of knobs?
Kuramoto: We suggest appropriate designs based on information from mechanical engineers and requests from a product planning section, or we come up with a completely new design by ourselves; it’s all decided as we discuss in the mean. Starting from fixing the [product’s] direction, we discuss and consider feasibility such as “this looks cool but hard to manufacture” or “it’ll be difficult costs-wise”. If one designed turns impossible, then we draw an alternative in a next design phase, suggest it, then bring it as close to our ideal.
Nagata: For the size of parts, sometimes we suggest, other times the design team do. Now that we have a 3D printer, we can make life-size parts right away.
Kuramoto: For example, knobs for the Filters was first as big as the ones in DJM-900NXS2. But as we decided its style was going to be the same as DJM-2000’s (sweeping to the right), it realized that “we can’t twist it all the way to the end with this thickness”, resulted in changing this thinner type just before we started making a mock-up.
Knob prototypes made by a 3D printer
Speaking of its usability, weight and smoothness of the Channel Faders have improved, haven’t they? Did you also add mechanical parts to electric parts here?
Nagata: Exactly. Their touch feelings were also adjusted with grease and mechanical parts. Actually, we had feedbacks that it’s difficult to made fine adjustments with DJM-900NXS2’s Channel Faders. The reason being, there is a bump-ish feeling as you touch them, causing them to move too much and making it harder to adjust by 1mm. On top of that, they often rattle, so we had rooms for improvements there.
DJM-V10 is a mixer focused on accurately mixing tracks, so just like the case of Master Isolator, what we wanted to achieve was a satisfying usability: being able to finely adjust by 1mm with Faders, rattles less and more sturdy. Personally, my goal was to achieve the same usability of mixing tracks with channel volumes in rotary mixers in our Faders. Faders are something we have particularly poured our efforts, we repeated the process of “prototype, measuring weight, collecting feedbacks, improved prototype” for about 3 months until we reached have we have now. I’m sure you can feel massive improvements from DJM-900NXS2. We’ve benefited a lot from our initiative of combining electric and mechanical parts.
Montpetit: I believe it’s only us who attach mechanical parts to electric parts.
Nagata: It’s very rare to design operation elements this meticulously, which makes it our competence. Unfortunately however, you can’t really tell the differences only with explanations, until you actually get your hands on it. [laugh] This [combination of parts] improved touch feelings, and durability too. By adding mechanical parts, electric parts are not directly loaded. This simply extends its life.
How often do you conduct durability tests during the development?
Nagata: We conduct durability tests extensively for newly adopted parts and operation elements. Let’s take a Channel Fader as an example: first we hypothesize “how many times it’ll be used per track”, then “for one hour”, “for one week”, also calculate “on a weekend” considering this’ll be a part of club standard equipment. Continuing this calculation in a year scale and you’ll get hundreds of thousands [of use cases]. Here, we use a durability test machine to see if parts won’t physically break down, or if electric signals can be still transferred, after being operated this amount. We cannot tell you the exact number for Channel Faders [testing], but you can imagine a tremendous amount judging from the official operable number of 10 million time for Magvel-Fader in Cross Fader. It’s such a surreal scene where a machine just rigorously goes up and down over and over. [laugh] [We also have] a machine just to twist a knob, or a machine just to press a button.
A fader prototype
Kuramoto: Those machines make terrible noises so we have a dedicated room for durability tests. [laugh] I rarely go there, but when I do go for some works, it’s such a bizarre place.
Montpetit: When we estimate these numbers, we always consider the worst case which to be honest can feel like “who would ever touch it THIS much?”. But since our product planning and development teams are the ones who must answer [results] in numbers, we need to assess very strictly. We are very proud of [our products’] durability which has passed those numbers of tests.
Next page:【 Exclusively designed Compressor for DJM-V10: control sound pressure intuitively with only one knob 】